Drums are a membranophone family of musical instruments that play a vital role in the Ghanaian setting.
Made in different sizes and shapes, these drums are put together to produce various indigenous music, ranging from 'Borborbor', 'Agbadza', 'Kpalongo', and 'Adowa' among others.
In this Ghana month feature, JoyNews’ Fred Quame Asare takes us on a journey through how these drums are produced to perfection.
Benjamin is one of the numerous drum cavers in the South Dayi District town of Peki, in the Volta Region.
He narrates that the drum-making process starts with finding a suitable tree in the forest.
Tsruboa is the most preferred in the locality here because of its durability.
The trunk is chopped into preferred sizes and lengths, to begin the process.
A caver needs a set of special tools to produce perfect drum pieces.
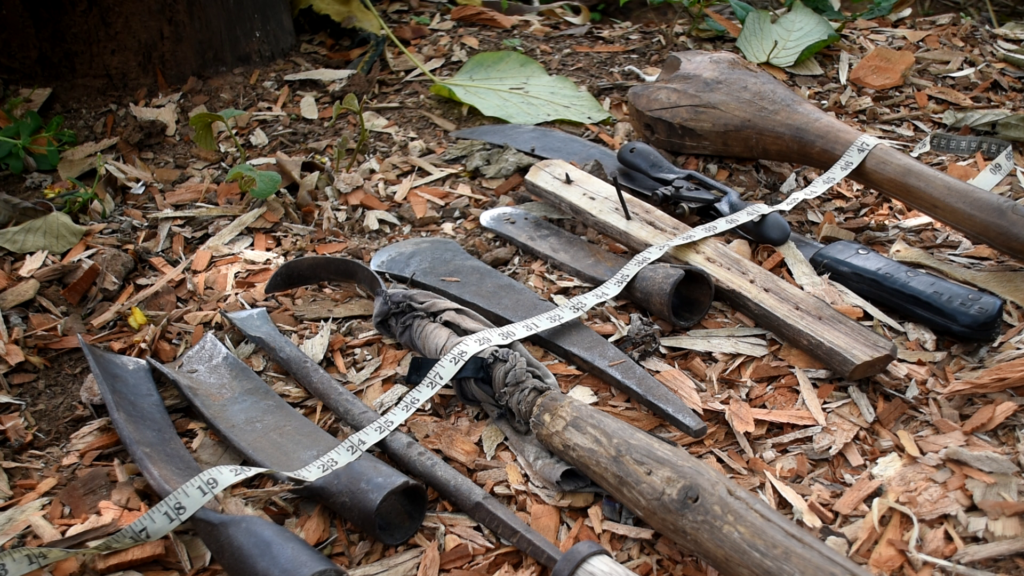
“I learned how to cave drums by observing carvers in the enclave during my childhood. A lot of people have trained under me and now have their production units", Benjamin narrates.
Today, Benjamin is caving a drum mostly assembled with other drums in performing 'Borborbor', and choral songs among others.
He first takes off the bark at both ends of the wood and then removes some portions of the hearth wood and growth rings, creating a hole in the middle of the wood.
The phloem, cambium, and bark in the middle are removed with a machete, carving the wood into a desired shape.
The rest of the hearth wood and growth rings and portions of the sapwood in the middle of the wood are removed. He continues until he gets the right measurement for his drum.
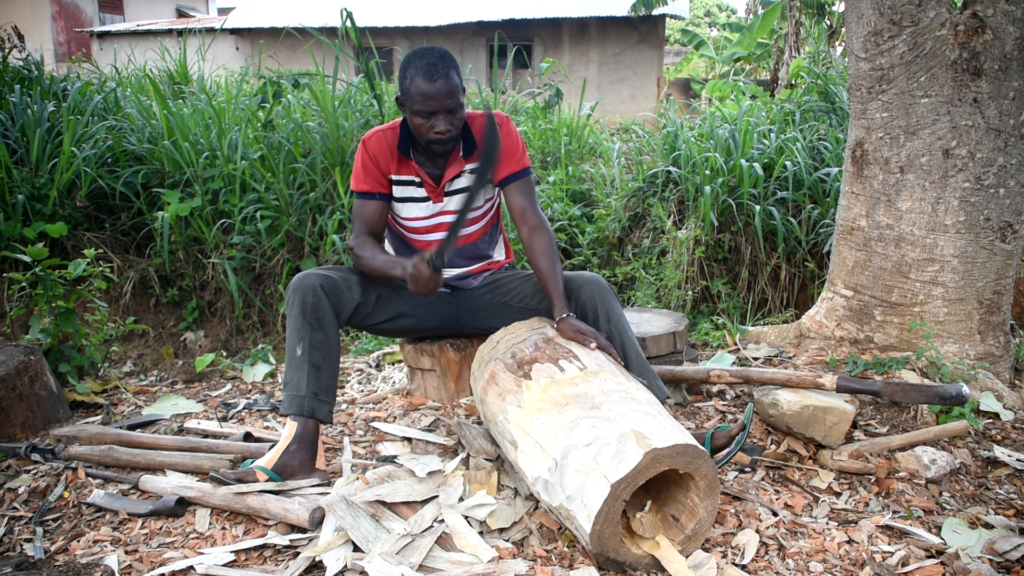
“When you are learning the skill, we guide you through the process little by little. Sometimes we allow creating a hole in the middle of the wood. We will do this until you become perfect at carving the drum", he chipped in while carving the drum.
He marks the drum and drills holes for the pegs which are used to control the sound produced by the drum.
A gage is used to draw lines around the drum, after which the service of a chisel is employed to design the drum. He adds dye to make the design visible. This project the beauty of the drum and makes it attractive.
Antelope, goat, sheep, and cow skins are stretched over the drum and tightened through with wooden pegs intertwined to the skin with a rope to form the drumhead.
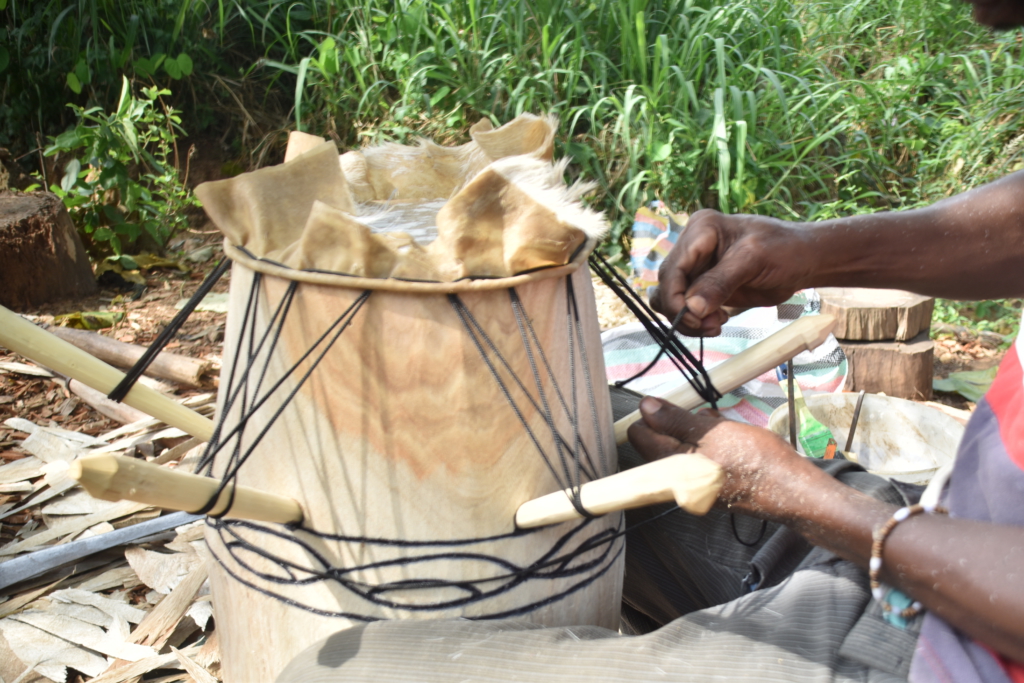
While working on the drum, Benjamin advised that the carver must be careful with the tools because they are very sharp, "and they hurt badly. You can get hurt at any stage of the process”.
After fixing the drumhead, the drum is painted and dried under the sun, after which it is displayed at a selling point along the Peki Asikuma-road.
The bigger the drum, the high the production cost and selling price.
Cavers in the Peki enclave identified a lack of capital as a major setback to their business.
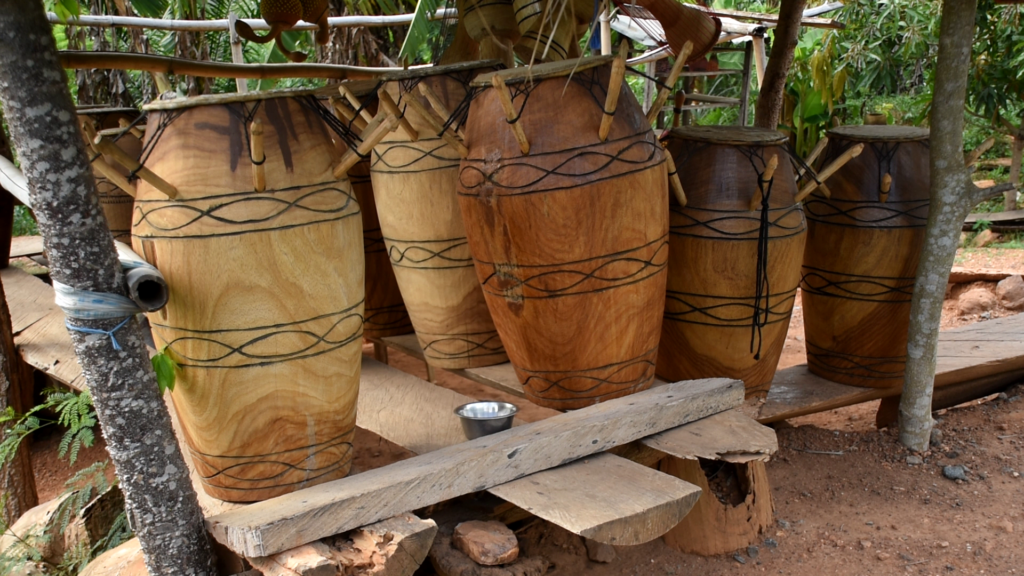
“They are buying the drums but we don't have money to produce enough for people to buy instantly when they visit our stands. When we have enough capital, we will produce all the sizes and types and display them so they can buy for us to get money and look after the family.
For Agbadza, we sell the five drum set at ¢5,000 and the four set at ¢4,500," said Akakpo Mensah, one of the carvers.
Latest Stories
-
BoG confirms GH¢2.14bn loss under Gold for Oil programme
17 minutes -
Photos from 2025 Absa Black Star Marathon
26 minutes -
Sarkodie pays tribute to Daddy Lumba: “The legacy lives on”
35 minutes -
Exciting offers draw crowds to Day 2 of Ecobank-JoyNews Habitat Fair in Tema
36 minutes -
Celebrities, politicians pay glowing tributes to Ghanaian music icon Daddy Lumba
52 minutes -
Bawumia mourns the passing of highlife legend Daddy Lumba
1 hour -
Tributes pour in for highlife legend Daddy Lumba following his death
2 hours -
One stabbed to death at China City Mall in Kumasi
2 hours -
Auditor-General’s Report: We have normalised corruption, theft and scandals – Prof Abotsi
2 hours -
Highlife legend Daddy Lumba passes away at 60
3 hours -
Ghana’s Koogo Atia wins men’s 42km as Kenya’s Nancy Githaiga claim women’s title at 2025 Absa Black Star Marathon
3 hours -
Raphael Botsyo Nkegbe dominates wheelchair 42km race at Absa Black Star Marathon
3 hours -
Deloitte Africa unpacks Mid-Year Budget Review – Watch Yaw Lartey’s full analysis
3 hours -
Take politics out of anti-corruption institutions – Dr Oduro Osae
4 hours -
President Mahama hails Black Star Marathon as key to Ghana’s tourism growth
4 hours